November 18, 2024
The steam engine was one of the most important inventions of the Industrial Revolution and it powered that revolution for over a century. But with the dawn of the twentieth century, steam power was vanishing and slowly being replaced with electricity. At the beginning of the new century, the Bingham Canyon Mine had a myriad of steam shovels and steam locomotives moving ore and waste out of the Oquirrh Mountains, but that was soon to change.
In 1916, the Utah Copper Company (UCC) sent a representative to Montana, who spent two weeks studying two electrified railroads: the Chicago, Milwaukee, and Saint Paul and the Butte, Anaconda, and Pacific. The representative stated that the “success of the system is unquestioned …” (Salt Lake Mining Review 1916:34). In 1921, UCC was operating 49 standard-gauge and 11 narrow-gauge steam locomotives (Strack 2022a). Seeing the potential of the new electrified railroad technology, UCC purchased its first electric locomotives in June 1924. They were put in service at the Magna and Arthur crushers, both of which had been electrified in September 1924.
Before the large-scale replacement of their steam locomotive fleet, however, UCC focused on the electrification of their steam shovels. In 1921, UCC was operating 21 steam shovels (Strack 2022a). The first railroad-type steam shovels were put into operation in 1906 by UCC and Boston Consolidated at their respective mine locations. In 1910, the two companies merged under UCC (Strack 2022b). Steam shovels consisted of a boiler and shovel mechanism mounted to a platform which was attached to a heavy-duty flatbed railroad car.
Operating a steam shovel was costly when compared to those operating on electric power. Excavating with steam-powered shovels required the maintenance of two sets of parallel running tracks: one for the shovel and one for the trains (Strack 2022b). A four-man crew was needed to maintain and laydown track so the shovel could move forward. In contrast, electric shovels were mounted on crawler treads (or tracks), like those found on bulldozers. This offered a great advantage over railroad-based steam shovels as the treads allowed unlimited mobility within the pit area (the area being excavated by the shovel) (Hodges 1925; Strack 2022b). In addition to mobility restraints, steam shovels required coal and water to operate, both of which needed to be brought to the shovel location on a regular basis. During idle times, a watcher needed to tend the shovel to keep the steam up. Repairs could be costly, and boilers periodically needed to be repaired and washed. Finally, electric shovels offered greater capacity and efficiency over steam shovels. Steam shovels were equipped with a 3-yard dipper (or bucket), whereas electric shovels had a 4.5-yard dipper. This larger bucket capacity allowed electric shovels to load a 48-tons capacity ore car in only four-and-a-half minutes. Similarly, electric shovels were more efficient in manpower, as it took ten men to operate a steam shovels, whereas three could operate a shovel powered by electricity (Hodges 1925).
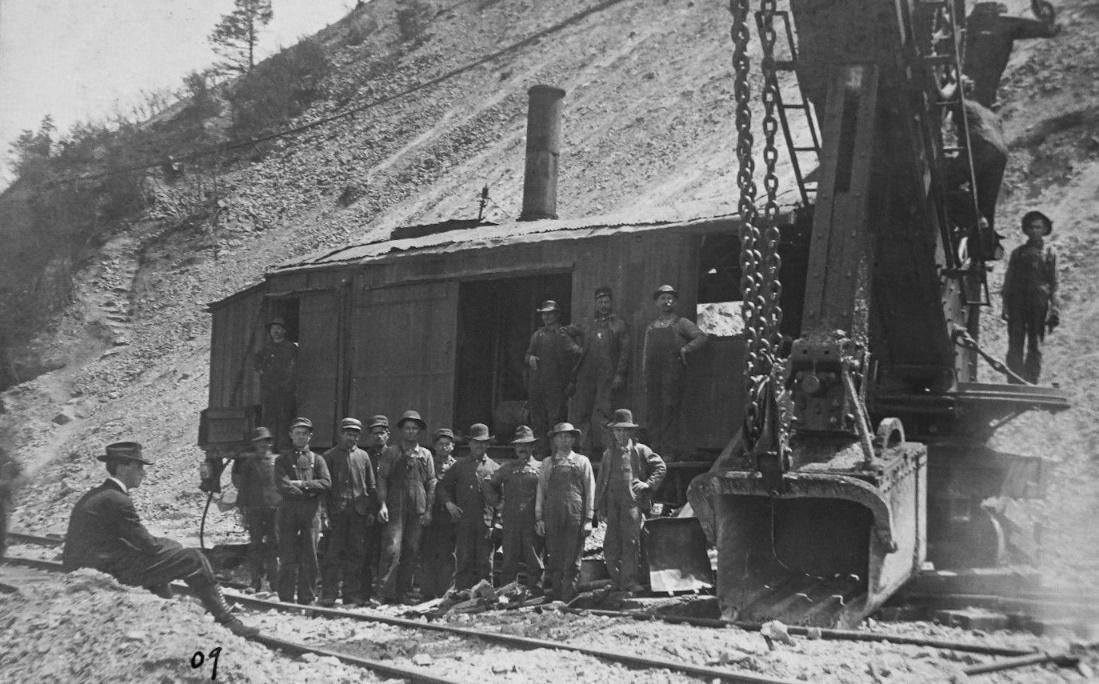
Steam shovel at UCC with crew and others (Lloyd 2022a).
In 1922, the first electric shovels were tested at the Bingham Canyon Mine; both were Marion Model 92s mounted on four roller tracks, each with 4.5-yard dippers. One operated on alternating-current (AC) motors and the other on direct-current (DC) motors (Strack 2022a; Strack 2022b). In January 1923, UCC announced that it would convert 20 of their steam shovels to electricity and that they planned to order 2 new electric shovels. The new shovels arrived in late 1923. Both were Marion Model 92s, one DC powered (Shovel No. 22) and the other AC powered (Shovel No. 23) (Strack 2022b). By late April 1926, all the shovels (new and converted) at UCC were running on electric power. In 1927, UCC had 23 electric shovels in operation (8 AC and 15 DC) (Strack 2022a; Strack 2022b).
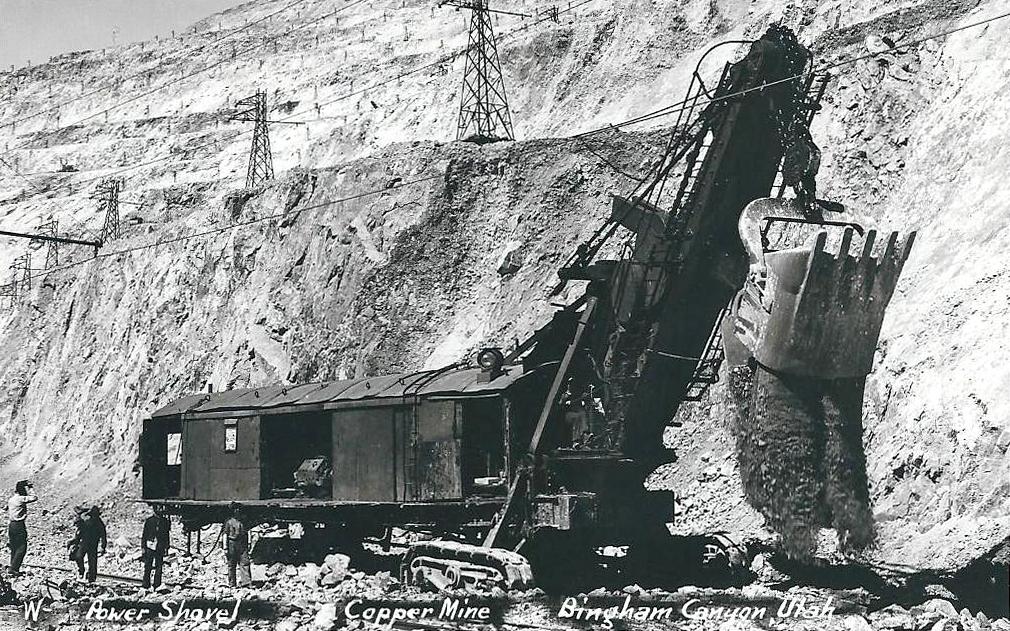
Steam shovel converted to electric power at Bingham Mine (Strack 2022c).
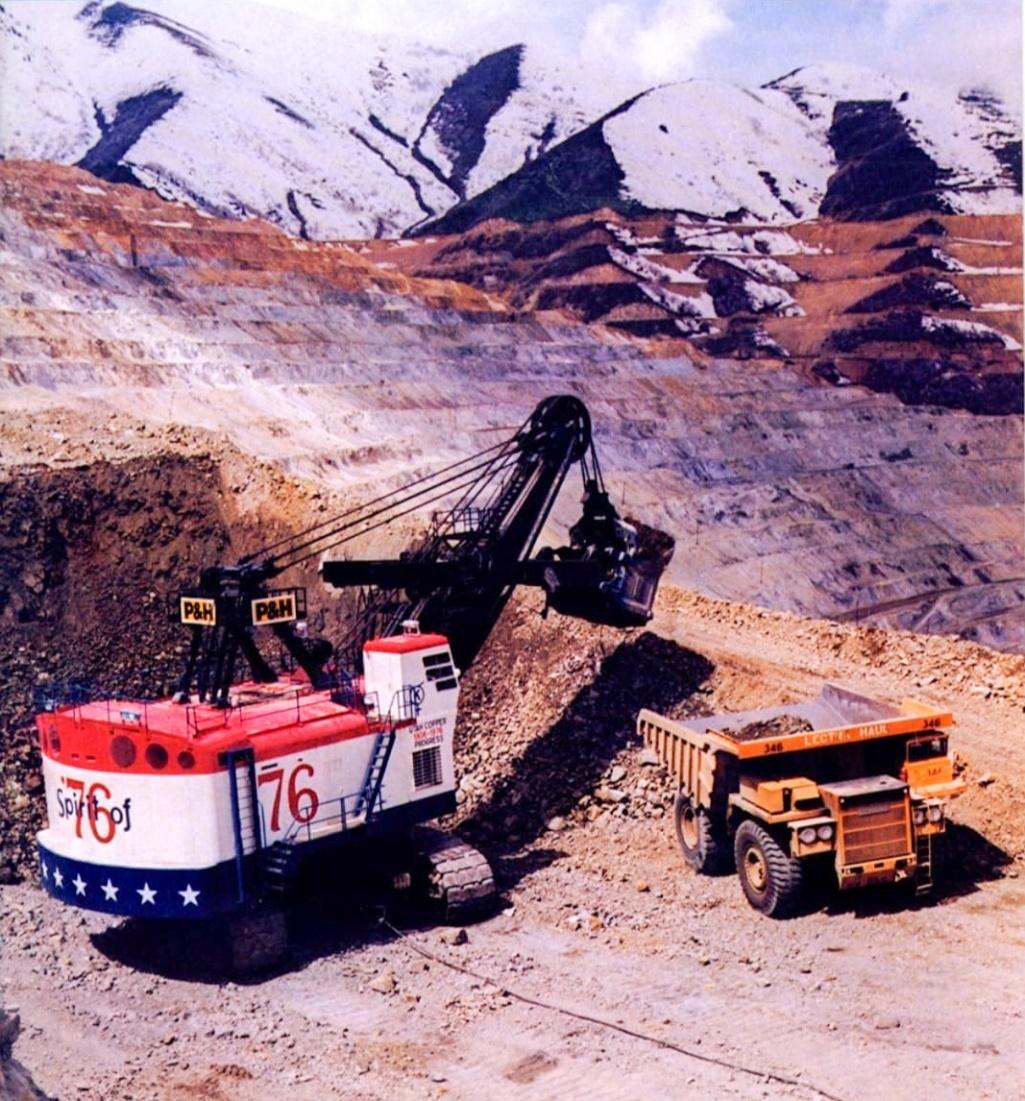
Modern electric shovel painted to celebrate USA 200th birthday, ca. 1976 (Ross 2022a).
Following the switch from steam to electric power for the shovels, UCC set new production records. In 1926, UCC produced 235,000,000 pounds of copper, breaking the previous record of 214,592,733 pounds set in 1924 by nearly 10 percent. On November 19, 1926, an ore shipping record was set when 55,300 tons of copper ore were shipped to the mills at Magna and Arthur in one day. All hauling records were broken on June 22, 1926, when 107,000 tons of ore and waste were shipped in one day. Consequently, mill tonnages increased as 48,400 tons of ore were treated on November 19, 1927, and the Garfield and Magna flotation plants averaged 45,500 tons a day for the month of November. As a result of these improvements, production costs during the third quarter of 1926 were reduced to an impressive 7.8 cents a pound, the lowest operating costs since 1915 when costs were 7.56 cents per pound and labor and supplies were considerably cheaper (Salt Lake Tribune [SLT] 2 January 1927:32).
Although electric power was available at both the Bingham Mines and the mills at Magna and Arthur, the available power was not enough to supply the 23 electric shovels already operating in the pit and the expected influx of new electric locomotives. In June 1928, UCC cleared an area above the Bingham and Garfield Railroad Yard in Bingham in anticipation of the construction of a new electric distribution center, comprised of two brick buildings, a cooling tower, and a substation. The new substation would be the second substation in Bingham. UCC already had five substations at the Magna and Arthur Mills and a power station, also located at Magna. Utah Power and Light (now Rocky Mountain Power) supplied 130,000 volts AC to the UCC power station, at which point it was stepped down to 44,000 volts AC and distributed to the substations. At the Bingham substations the voltage was reduced to 550 volts AC and then transformed to 750 volts DC for use by the shovels and locomotives working in the pit (Strack 2022a).
As mentioned earlier, UCC already had two electric locomotives operating at the Magna and Arthur crushers, the yards having been electrified in 1924. Following the electrification of the shovels, UCC ordered two electric locomotives for testing in late April of 1926. One was an oil (diesel)-electric locomotive (No. 600) and the other was a combination electric trolley/battery type locomotive (No. 700). Testing of the two different types of locomotives began on May 16, 1927. The combination type locomotive (No. 700) was preferred and on May 8, 1928, UCC ordered 20 new locomotives, with the intent to eventually replace all steam locomotives (Strack 2022a).
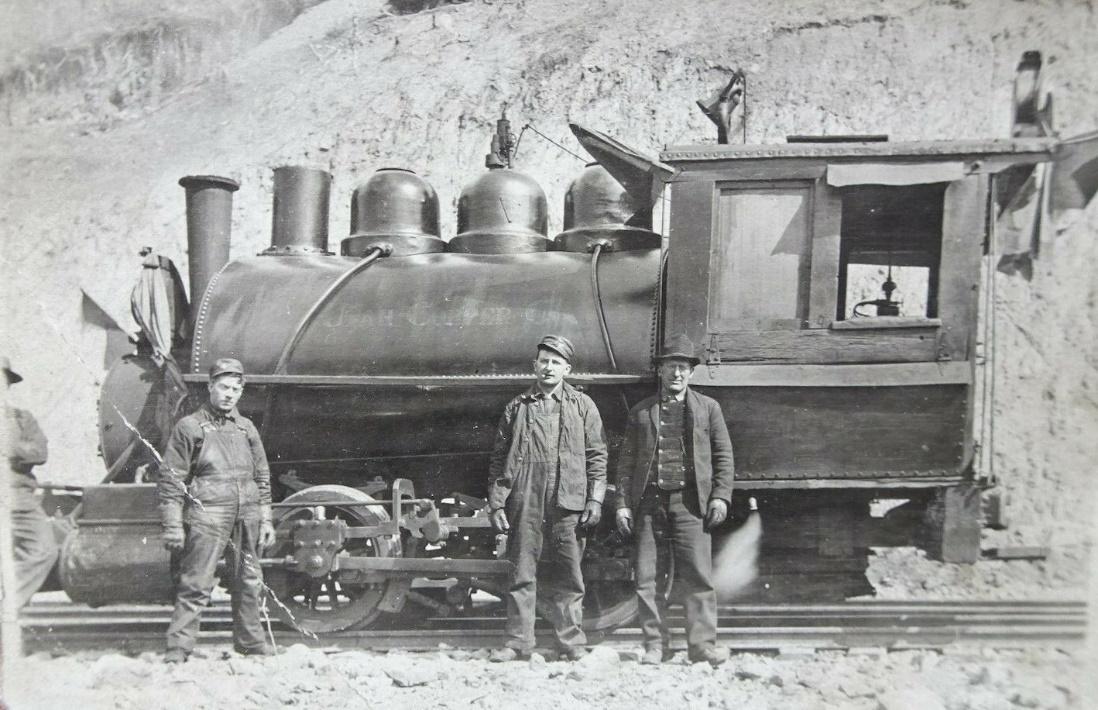
UCC steam engine, middle crew member may be John Peter, crew member on right may be Fred Cox, a faded “Utah Copper” is stenciled on the boiler (Lloyd 2022b).
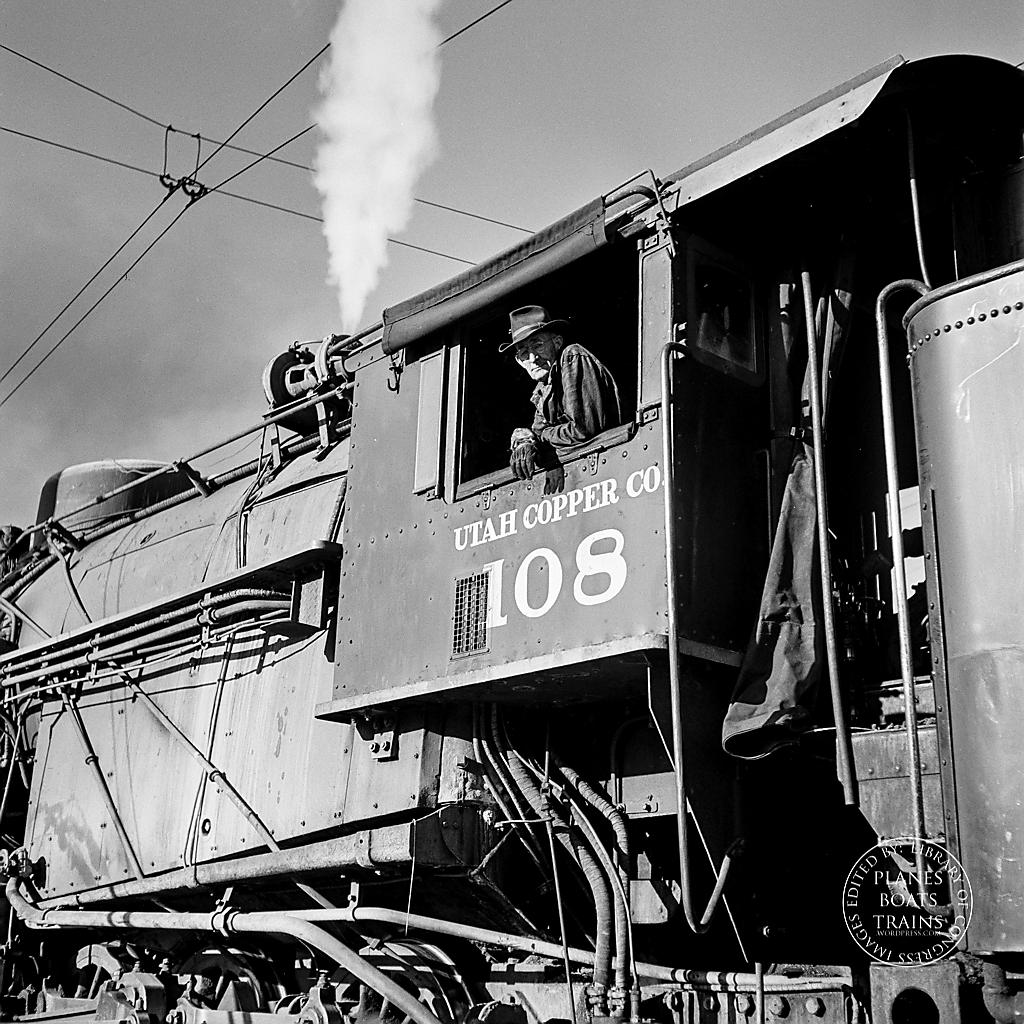
Close up view of UCC steam locomotive cab (Ross 2022b).
The first of the new locomotives (No. 702) arrived in September 1928. Locomotive 701 never made an appearance at the Bingham Mine, having been wrecked during transit. By October 1929, UCC had 41, 85-tons electric locomotives, numbered 700 to 741, minus 701 of course. In early 1929, total electrification of the Bingham Canyon Mine was complete and a new one-day ore and waste hauling record of 141,000 tons was achieved on May 16, 1929 (Ogden Standard-Examiner [OSE] 19 January 1930:2).
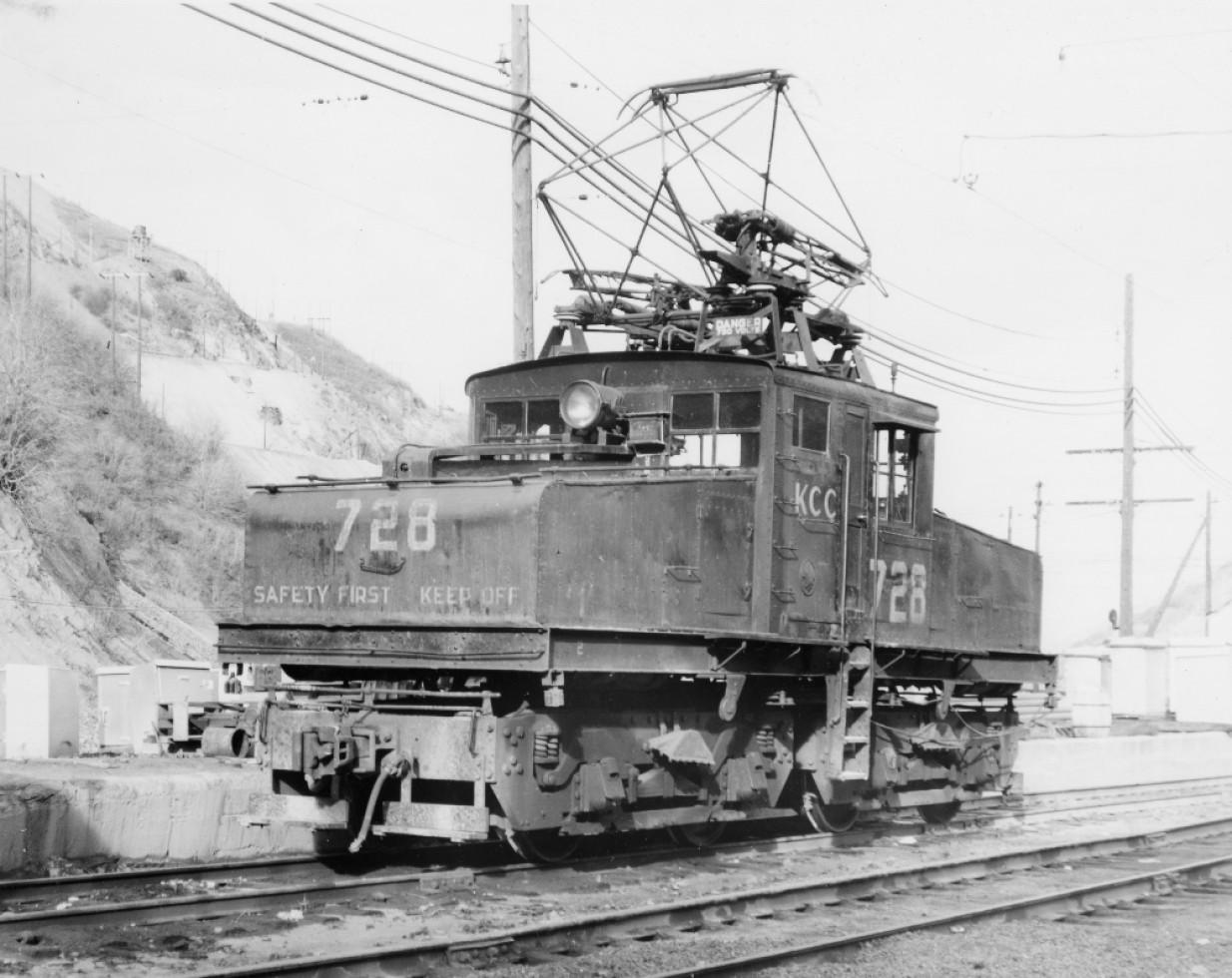
Eighty-five tons electric locomotive 728, 1961 (Davis 1961).
By 1989, the train service at the Bingham Mine (then operating as Kennecott Copper Company [KCC]), was hanging on by a thread, and the few locomotives that were moving the trains were diesel. The reason for the decline in rail service was that in 1984, KCC had lost $160 million due to low copper prices, and on March 26, 1985, KCC was shutdown. The shutdown resulted in 5,000 employees losing their jobs. Eight months later, it was announced that KCC would reopen, with a reduced workforce of 1,850 employees. Mining operations were to be modernized and part of that modernization was the elimination of the obsolete and costly train service. Operating and maintaining locomotives, rail cars, track, and the numerous employees that were needed to operate a train system was expensive, especially when compared to the future vision of conveyor belts and pipelines that could be manned by a dozen people (Kooistra 1989).
The modernization was completed in early 1988 and the train service was slated to become a thing of the past; however, fate intervened when copper prices tripled, and the retention of the train service was seen as a means of keeping production and profits high. It was announced on March 12, 1988, that the train service would operate as long as copper prices stayed high. Unfortunately, the trains fate was sealed, and they were eventually phased out (Kooistra 1989).
Although the current shovels operating at the Bingham Mine today are still powered by electricity, the train service is gone, having been completely replaced by the conveyor belts, pipelines, and gargantuan haulage trucks in the early 1990s. This change resulted in a complete overhaul of Bingham Mine’s electrical infrastructure and greatly reshaped the topographical architecture of the pit.
Credits
Grant Fahrni, Logan Simpson