November 18, 2024
Before the advent of open-pit mining in the Oquirrh Mountains, mining operations almost exclusively occurred underground. Underground mining is a dirty, physically demanding, and dangerous occupation that requires special skills to perform. Dangers were many and included “scalding water, plummeting cage elevators, cave-ins, fiery explosions, toxic air…” (Weicksel nd), and a myriad of other hazards which often resulted in scarring, paralysis, and death (Mulcahy nd; Twitty 2009; Weicksel nd).
A light source was crucial for underground mining, for once below the surface, the darkness was absolute. Prior to the days of fuel-charged miner’s lamps and electricity, a candle was the sole light source for miners. At the start of each shift, the miners grabbed a handful of candles that served as their light sources throughout the day. Candles were ensconced in simple, metal candlesticks, often referred to as “Sticking Tommies”, which consisted of a circular candleholder with a spike and sometimes a hook, that could be attached to the miner’s hat, or pounded into timbers or cracks in the rocks. Miners typically owned the candleholder but usually had to pay for the candles they used during their shift (Pearson 1996; Pearson and Bommarito 2002).
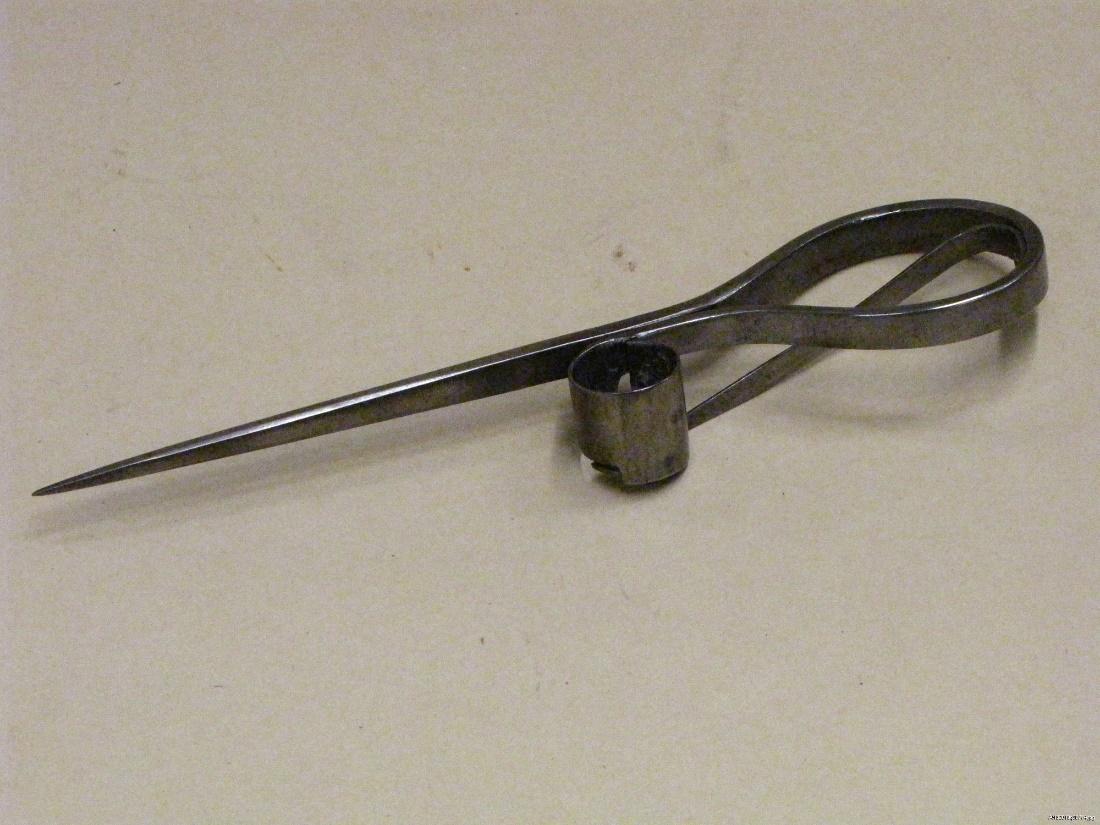
Sticking Tommy used for holding candles during a miner’s shift (Weicksel nd).
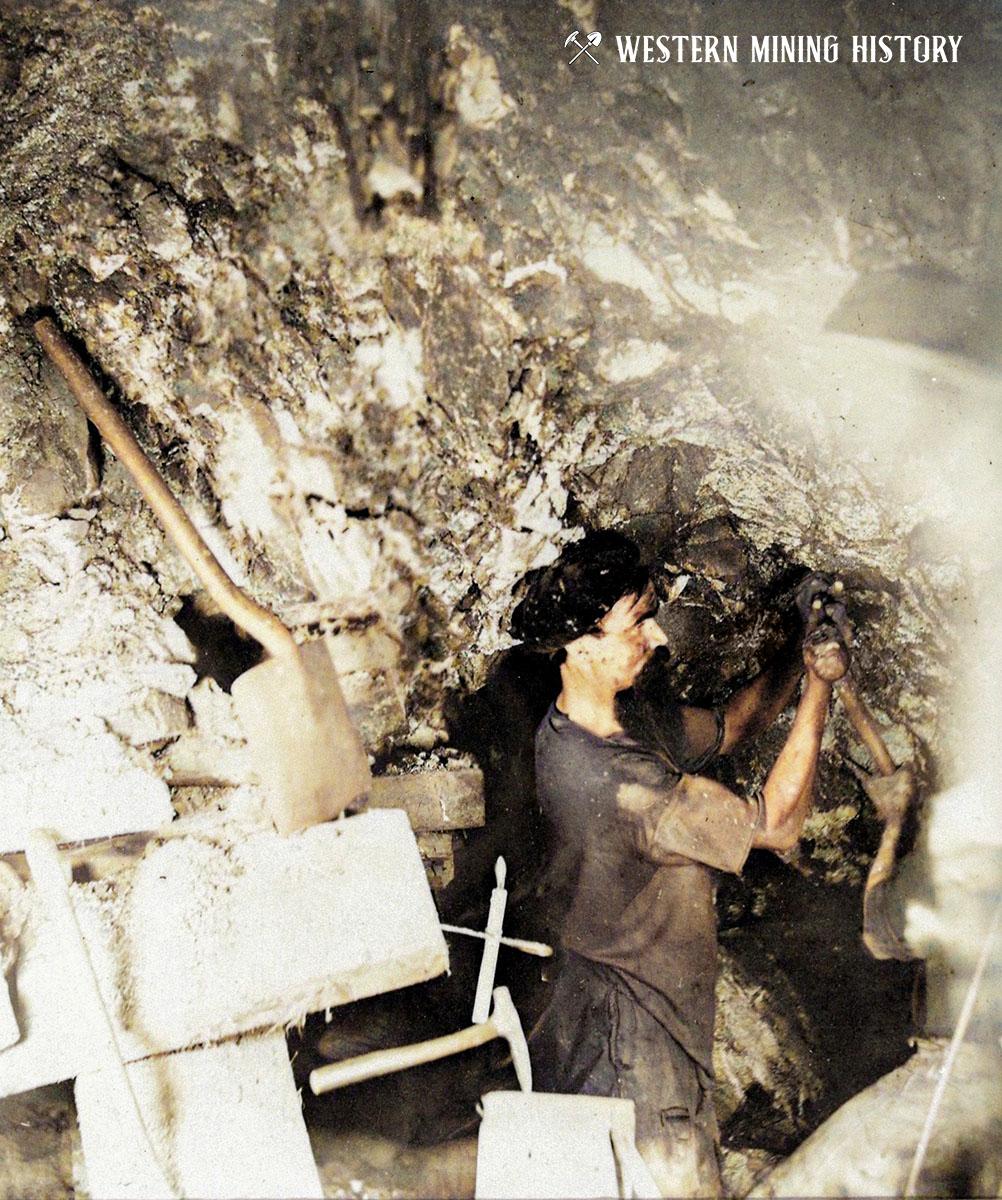
Colorized version of two miners double-jacking by candlelight 1867 (O’Sullivan 1867).
Mine workers were divided into surface men and miners. The surface men cut timber, built machinery, cleared land, set up tramways, and moved waste rock. One of the key occupations of the surface men was the blacksmith, who sharpened drills and repaired metal items (Rakestraw 1965). Miners included drillers, powdermen, shaftmen, muckers, timbermen, trammers, motormen, skip tenders, and trackmen; chief among them were the drillers and blasters (Graeme 2013; Twitty 2009).
Drilling and blasting historically played a major role in the mining industry and continues to play a significant role in current mining operations. During the Industrial Revolution, incredible technological advances were made in the excavating of mines when labor intensive hand drilling was replaced by pneumatic drills that operated on compressed air produced on the surface. Prior to the pneumatic drill, the boring of blast holes into bedrock consisted of a miner who wielded a single-jack (small 3-to-5-pound hammer) and a short drill steel or a pair of miners who worked in tandem known as double-jacking. Double-jacking consisted of a two-man crew, where one miner (hammer swinger) swung a long-handled sledgehammer (7 to 10 pounds) while the other (shaker) held a drill steel that he would turn slightly after every strike. Double jacking took great skill and an abundance of confidence in your partner. On occasion, triple-jacking would occur, where two miners swung hammers; however, this was a rare occurrence, since typically there was barely enough room for two miners, let alone a third (Nuggets of News Blog 2014; Twitty 2009). During a 10-hour shift, 8 to 10 holes could be drilled, each hole measuring 8 to 10 inches deep. Blasting took place at the end of the day when the drill team filled the holes with black powder (blasting powder), attached the fuses, and eventually lit the fuses, setting off the blast. Approximately three-quarters to two tons of rock would break away and be ready for removal to the surface (Nuggets of News Blog 2014; Twitty 2009).
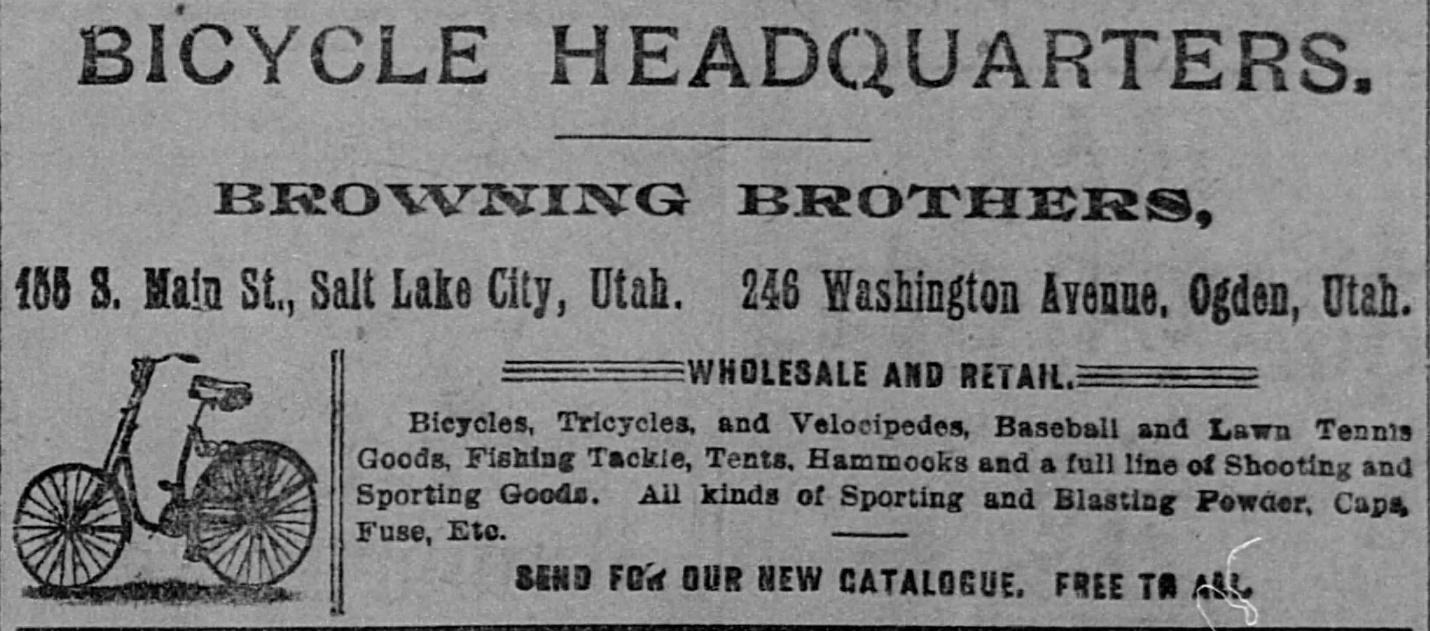
While picking out a bicycle, shoppers could also stock up on blasting powder and other blasting accessories, 1892 (Salt Lake Herald [SLH] 14 September 1892:5).
Prior to the mid-1860s, black powder was the only explosive available to the mining industry. This changed with the invention of dynamite in 1866 by Alfred Bernhard Nobel. By the end of the 1870s black powder was largely replaced by dynamite as an explosive for mine use (Nuggets of News Blog 2014; Twitty 2009).
Blasting is a dangerous occupation and the safety guidelines recommended by mining and explosive experts were frequently ignored. The first and most important step in explosive safety was proper storage. Improperly stored explosives degraded and became unstable, especially dynamite. Mining and explosive engineers recommended that explosives, both blasting powder and dynamite, be stored in a separate building (magazine) that was bullet-proof, fire-proof, dry, well ventilated, protected from extreme temperature fluctuations and used only for the storage of explosives. It was strongly recommended that containers never be opened within the magazine and that the floors should be kept free of any leaked nitroglycerin or spilled blasting powder. As an added precaution, detonators and fuses were to be stored in a separate facility. Money often determined whether explosives would be stored correctly as only the largest and most profitable companies could afford the expense of an adequately built magazine. Most small-time operations could not afford the expense of an additional building, let alone a magazine that was used only for storage of explosives (Twitty 2009).
Handling and deploying black powder and dynamite was a risky occupation and accidents were a common occurrence. The precautions and steps for the safe handling of blasting powder were basic: do not open kegs near open flames, do not smoke while in the vicinity of the powder, do not use metallic objects that could produce a spark, and handle gently. As with the storage of blasting powder, however, these recommendations were frequently ignored. Early on, blasting powder came in wooden kegs equipped with threaded bungs (stoppers) that were frequently not replaced after the keg was opened. These kegs were usually undamaged because a rebate was available for empty, undamaged kegs; however, when kegs were redesigned with a cleat tops and thinner walls, miners began opening the keg with a pick, an extremely dangerous practice given that a single spark could cause ignition (Twitty 2009).
The change from black powder to dynamite often proved problematic with old time miners who were set in their ways and thought the old ways of doing things were the best. Dynamite had to be handled differently than blasting powder and instructions on how to handle the new explosive were scarce. Most miners learned by trial and error, sometimes with deadly results. There are many differences between blasting powder and dynamite, the most notable of which is nitroglycerine’s (the explosive ingredient in dynamite) sensitivity to shock, especially when it has not been stored properly. Unfortunately, this was a characteristic that miners were often unaware, since some manufacturers claimed that dynamite could “… be tumbled about as safely as so many boxes of soap” and that it could “… be hammered between wood and stone, wood and iron, and sustain any shock“ (Twitty 2009:122). There were also claims it could be safely carried around in boots and pockets. Although special carrying cases were available for transporting both powder and dynamite, they were rarely provided by the mining companies (Twitty 2009).
As noted earlier, blasting occurred at the end of the shift. Each blast would be counted and any misfires (explosives that did not detonate) would be reported to the incoming shift. Misfires were extremely dangerous since some unfortunate miner had to reenter the blast area and extract the unexploded charge. There were many causes for misfires, including faulty blasting caps, poorly crimped caps, damaged fuses, or frozen dynamite. (Twitty 2009).
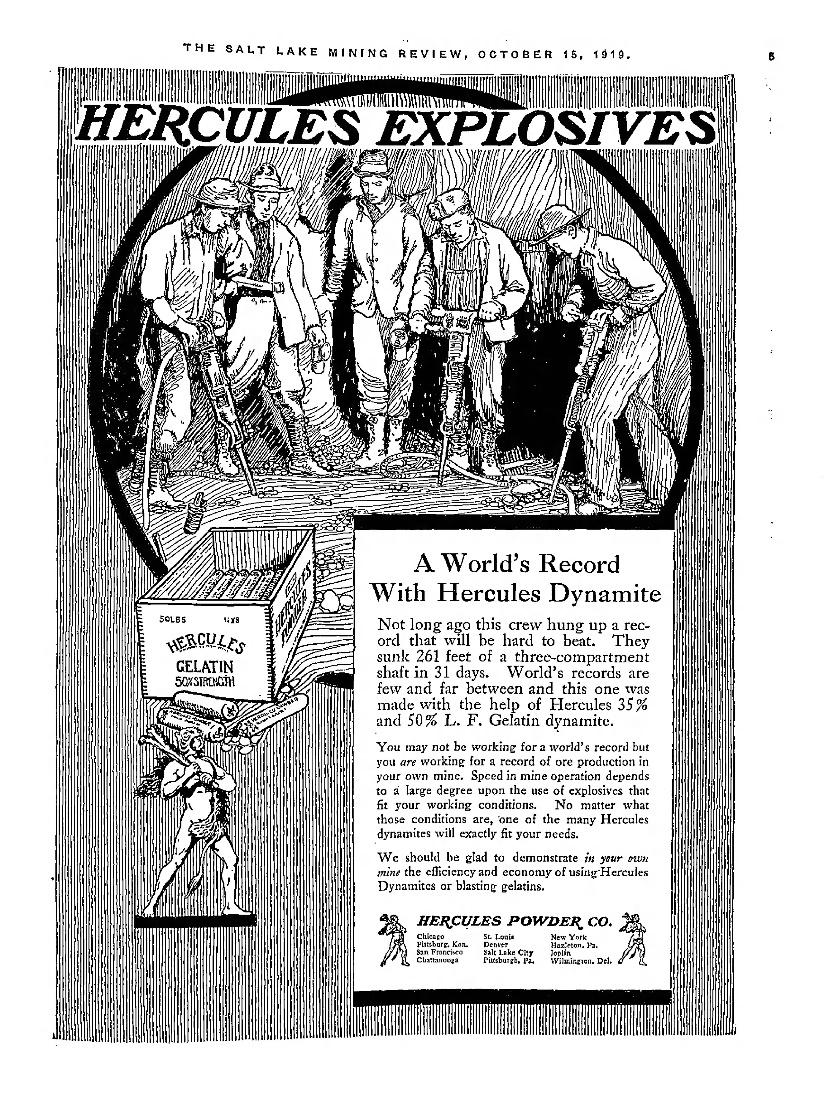
Advertisement for Hercules dynamite showing drillers 1919 (Salt Lake Mining Review [SLMR]. 15 October 1919:5)
The safest way to mitigate misfires was to drill around the unexploded charge, blast out the rock and then pick out the unexploded charge from the debris. Another method was to gently remove the tamping material from the hole, insert a new stick of dynamite and then blast both together. For the company, these methods were too time consuming, or they claimed the extra charge made the cliff face difficult to work. Companies preferred to clear out the hole by drilling, a dangerous proposition. On May 26, 1900, a miner named Davis and his two partners were informed by the previous shift of two misfires. The plan was to drill around the misfires and then pick them out after the blast. Unfortunately, there was a third, unreported misfire and the drill steel hit it, setting off an explosion that seriously injured Davis and killed his two partners. The best method to prevent misfires was through proper storage, handling, priming, loading, and firing (Twitty 2009).
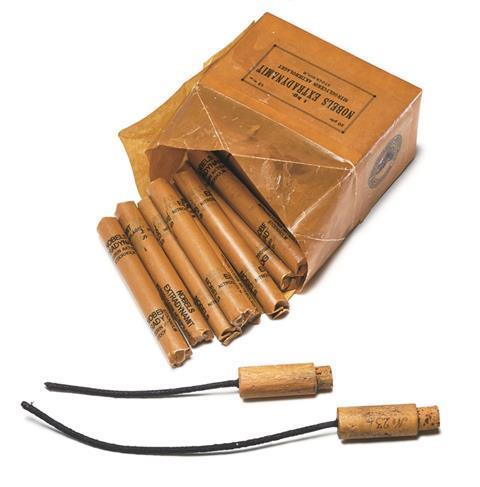
Nobel’s Extradynamit, 1875 (Wothers 2011).
Another technological advancement in the underground mining industry was the invention of the pneumatic drill, which was usually powered by compressed air from the surface, although on occasion steam would be used. One of the dangers of working with pneumatic drills was when a hose came uncoupled. If powered by steam, the miners were in danger of being scalded, or if powered by air, whipped, and pummeled until they could get the hose under control (Twitty 2009). This new technology allowed a two-man team to drill three-to-four-foot holes into the bedrock within minutes. The amount of rock that could be blasted loose rose from three-quarters to 2 tons per shift to 4 to 10 tons per shift. A two-man team could advance three to five feet per shift, whereas hand drillers only advanced one foot (Nuggets of News Blog 2014; Twitty 2009). A two-man crew was still necessary to operate the drill as they could weigh over 300 pounds. The crew consisted of a drill runner and a chuck tender, who changed out drill-steels, turned the steels, and cleaned out the holes. Eventually the steels were manufactured with a hollow center and air was forced air down the steel, thus automatically cleaning out the hole, but filling the chamber with clouds of dust (Twitty 2009).
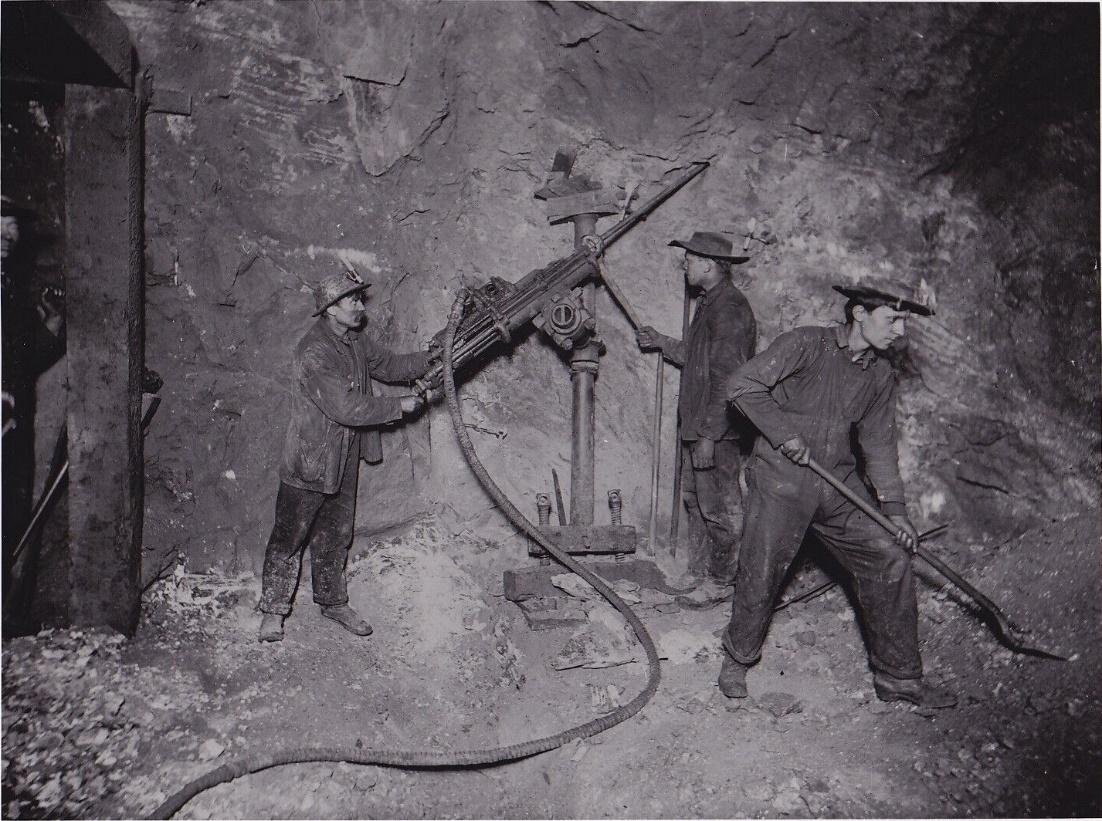
Drillers operating pneumatic drill in underground mine Bingham Canyon (Lloyd 2022).
These dust clouds had a devasting effect on the miners’ health. The dust was full of minute razor-sharp silica particles that when breathed into the lungs caused swelling and resulted in hardened and scarred lung tissue. Commonly known as miner’s consumption, silicosis is an incurable lung disease. Typically, it took 10 to 20 years to develop, and symptoms may not appear until years after the miner stopped working in the mines (NHS 2021; Nuggets of News Blog 2014). Among miners and their families, the pneumatic drill was called the Widow Maker (Nuggets of News Blog 2014; Twitty 2009). The dust clouds were eradicated by an improved drill that pumped water into the borehole, thus turning the dust into mud. An added benefit was that the water acted as a lubricant and cooled the drill bit. The trade-off for not having to breath the hazardous dust, was that the miners were now wet, muddy, and probably uncomfortable. This updated pneumatic drill setup is still used in mining operation today (Nuggets of News Blog 2014, Twitty 2009).
In the nineteenth century and early twentieth century, underground mining was a dangerous occupation for everyone involved, especially for drillers and blasters who had the added danger of handling explosive materials. Many of the accidents that occurred were preventable. Although many miners often had the opportunity to prevent accidents, carelessness, laziness, lack of proper training, haste, and pressure from mining companies to take shortcuts often resulted in miners making small mistakes that had deadly results. Most mining companies of the day prioritized production over safety. Fortunately, by the 1910s the number of mining accidents were greatly reduced as miners became more familiar with the handling of the new explosives, explosive materials were improved, and mining companies became an active participant in keeping their employees safe. By the 1930s, mining companies were frequently vying with one another to see who had the greatest number of days without an accident, a competition that led to safer working conditions and the continual reduction in mining accidents (Twitty 2009).
Credits
Logan Simpson