January 1, 1911
Moving a mountain requires large trucks with dump capabilities. Trucks in Bingham mine can load and unload nearly 400 tons of waste material in one go (Strack 2022a). Getting to this level of productivity and efficiency today involved an innovative series of growing trucks, diverse technological advances, and continual improvements.
Iconic to the mining era of the old West is the mining cart. Typically pulled by muscle—whether human or animal—these machines had many limitations. While horses and mules carried most of these early loads, their usefulness was limited as the work was grueling for these animals. The amount of ore that was able to be hauled was limited by the strength of the animal pulling the cart. The ore was then loaded onto wagons and train cars that were hauled many miles over rough terrain. Later, after the advent of the locomotive, ore was also transferred via dumping through chutes that towered above wagons and train cars.
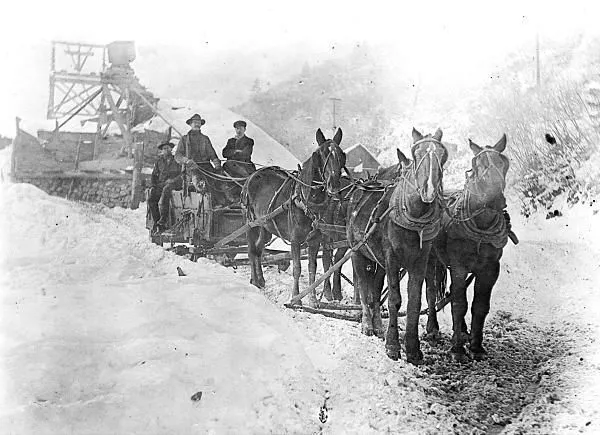
In 1911, after seeing how difficult and time consuming it was for an individual to unload a cart of coal, Garfield (Gar) Arthur Wood invented a hoist system that gave carts the ability to mechanically lift and dump its contents (Antique Boat Museum n.d.). Utilizing the new technology to mechanically lift and dump cargo, the birth of the haul truck or dump truck came in the form of the Model 1Z Trac-Truk, designed in 1934 by the Euclid Road Machinery Company of Cleveland, Ohio (Teague 2022).
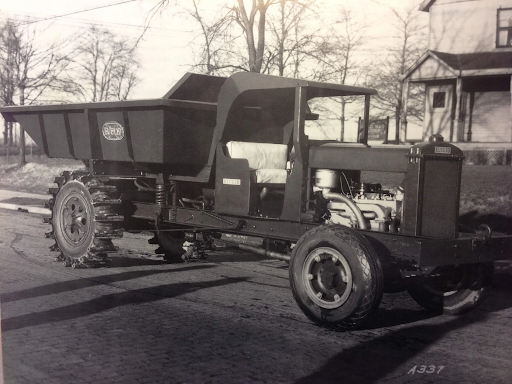
Off-highway trucks started showing up in the Bingham Mine in the 1950s. To move millions of cubic yards of waste material in the mine, Kennecott turned to Western Contracting and their massive trucks. The “World’s Largest Truck” arrived in December of 1958 on three railroad flat cars (Strack 2022a). These trucks and the overall contract were described as:
A real giant, comparable to something out of a Paul Bunyan tale, is hard at work hauling 100 cubic yards of earth at Kennecott’s huge Bingham open pit copper mine. It is the world’s largest truck and is owned by Western Contracting Corporation. Western’s head offices are in Sioux City, Iowa. They have the contract for stripping 8,000,000 yards of waste overburden from upper levels on the east and west sides of Kennecott’s Bingham mine. The operation will take ten months to complete (Strack 2022a).
Kennecott stated that utilizing trucks was much more practical than moving millions of tons of ore and waste rock via the 175 miles of railroad (Salt Lake Tribune [SLT] 16 December 1962:53). In 1963, Kennecott began to remove rails, replacing them with haulage trucks in the upper levels of the mine, “…because of limitations of rail haulage, along with advances in truck technology (Strack 2022a).” Five KW Dart models were the initial trucks used in Bingham Mine’s new truck haulage operations. These trucks were numbered 201 through 206 and could haul 65 tons of waste material (Strack 2022a).
In 1967, Kennecott purchased eight Lectra Haul Model Number M-100’s which could haul 100 tons of ore and waste material (Strack 2022a). The trucks continued to increase in number and capacity, and between 1974 and 1981, the haul truck fleet at the Bingham Mine increased to 62 Lectra Haul Model Number M-36’s that could each haul 172 tons of material. While many of these were purchased, 20 were leased. During this time, Kennecott also leased 25 Euclids R170s with the capacity of 150 tons (Strack 2022a).
By 1983, the Bingham Mine had converted to shovels and trucks only, leaving the age of the railroad behind. Trucks now hauled both the ore and the waste material (Strack 2022b). In the 1990s, Kennecott had 10 Komatsu 830E trucks. The Komatsu 830Es could haul 250 tons and were electric diesel trucks. These were later sold to another mine. Dustin (Dusty) Stauffer is a current mine equipment operator that comes from generations of miners. He described the evolution of truck usage at Kennecott:
“And we then also had 10 Komatsu 830E haul trucks. That were equivalent in size to the Cat 93B, but they were a diesel electric haul truck. Meaning it wasn’t the traditional standard mechanical driven truck with a transmission. So, you had motors that propelled machines, so that was kind of the start of the electric drive trucks. But they had experimented with them previously from talking with my dad. Back, I believe, even in the 70s to 80s, they had experimented with those types of electric drive trucks. And they weren’t very successful because they weren’t able to haul down the hill without going outside of the, what they call, the dynamic envelope (Dustin Stauffer Oral History Interview 2022).”
Later that decade, Komatsu 930E trucks, hauling 320 tons, and two Caterpillar 797s, hauling over 400 tons, arrived at Bingham. In the 2000s, Kennecott began to replace the Komatsu 830E trucks with 930Es (Strack 2022a). Kennecott numbered these Komatsu 930E trucks 450 through 459. These Komatsu had A/C drive wheel motor systems. Dusty Stauffer further explains the A/C drive:
“And that was actually A/C drive wheel motor system, which, there is a big, well, in my opinion as an operator, pretty big difference between a D/C drive system and an A/C drive system, which they are more, they react a lot quicker, and they seem to have a lot more power as well in that system. It pretty much scrapped the 830E Komatsu that they had, which were numbered the 401 to the 410 (Dustin Stauffer Oral History Interview 2022).”
Since the days of the mine cart, ore haulage capacity has grown from the limited amount of ore a single cart could carry to the trucks at Bingham Mine today which can carry a load of up to 320 tons (Salt Lake Tribune 2012). Technological advances in truck manufacturing and design have led to the transformation of mining from small scale underground operations to large scale open pit sites. Today, colossal dump trucks, towering up to two stories tall, haul millions of pounds of ore, making Bingham Mine the largest open-pit mine in the world.
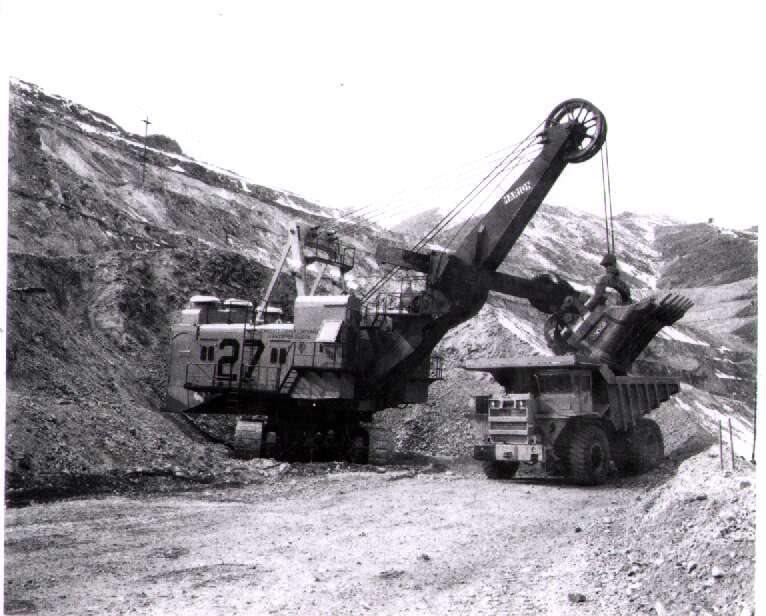
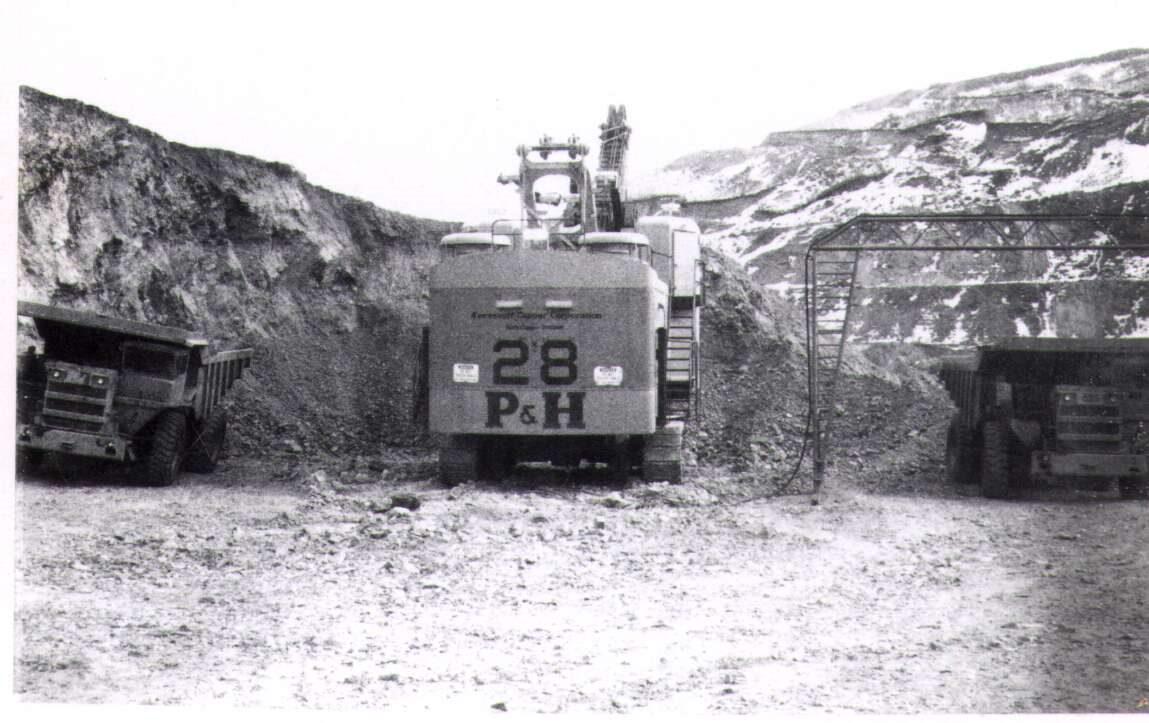
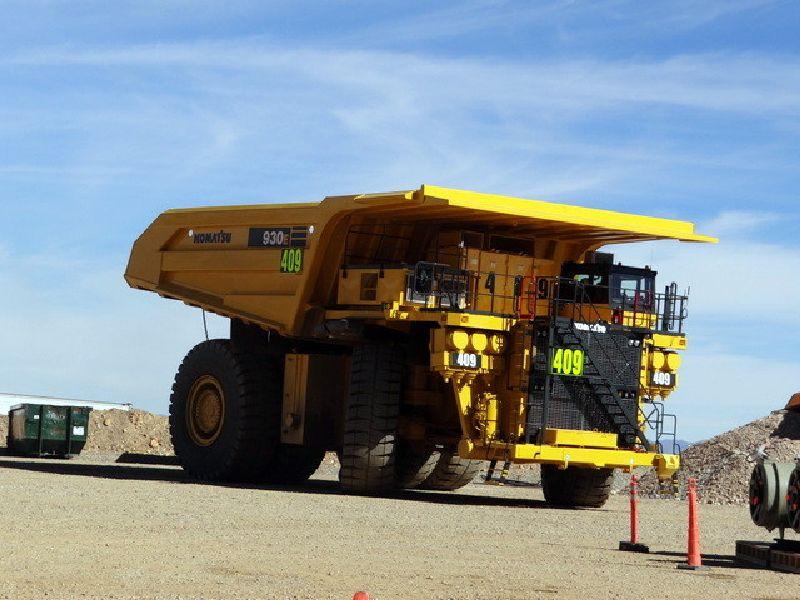